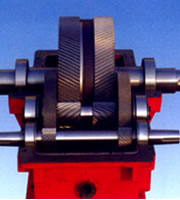
Introduction
The Shuangxin gear reducer utilizes tenacity iron housing, forged and high-tensile cast steel gearing, being greatly superior to the conventional cast and steel combination.
All Shuangxin gear reducer features precisely machined herringbone gears. The steel gear after heat treatment exceeds API criteria (mainly the pitting and bending stress). Our design allows extra wide gear tooth interfaces for uniform loading and equalized stress during peak torque operation.
A rugged, fully machined ductile iron case houses component gears, with a split centerline for easy disassembly while alloy steel shafts rotate in oversized precision roller bearings ensure that there is no bronze bushing to seize and no shaft wear from rotational contact.
In addition, there is no oil pump to fail or maintain. Add to that a generous center relief that ensures positive flow to all gear tooth interfaces and a submerged gear and wiper system which delivers a supply of lubricant to the oil galleries and you have a hardworking gear box of the highest possibly quality and craftsmanship.
Technical specification
1. Designation
(1) For domestic market
When place order, please clearly specify the total centerline distance, rated output torque, transmission ratio, etc.
The designation is as follow:
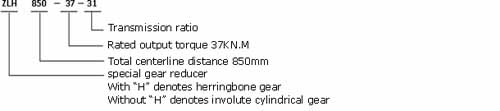
(2) For world market
When place order, please specify the total centerline distance, rated output torque, transmission ratio, etc.
Designation is as follow:
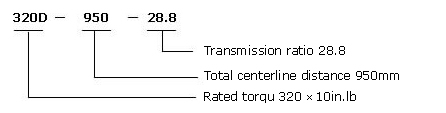
Illustration of structure
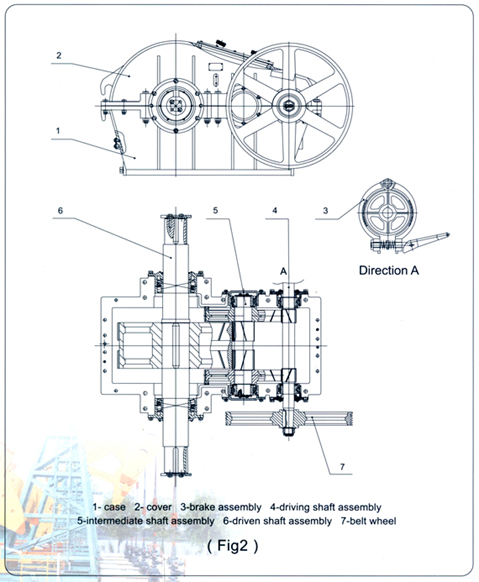
Structure introduction
The transmission of the reducer is implemented by herringbone gear or involute cylindrical gear (or double helical gear). Both driving shaft and the intermediate shaft are gear shafts. Left/right helical gear engage with stationary fit of key and shaft. Some driven shafts have both ends, matched with two keys perpendicular to each other, contacting the crank with taper key. After certain period running, turn the crank 90° to match with a new key to be fitted. In this way, the maxim load is shifted to the teeth with relatively less wearing, hence the life is prolonged. Seal at the shaft end consists of the embedded bearing cap, oil return hole, etc. The contacting surface of the case is coated with sealant. The oil stripper is fitted on the case seat near the beveled teeth, and lubricant channel is grooved on contacting surface of the case to lubricate the bearing.
On the top of the box cover is an inspection hole, with a vent cap on its top. When an alternative design, on one side of the case are three plugs at different heights, the lowest one is for draining oil, and the other tow are for checking oil level.
Repair and maintenance
* During installation, fill lubrication oil into the two bolt holes on the oil sump of the reducer case. Lubricant tag No. is 150# for extreme pressure gear oil in summer, 120# extreme pressure gear oil in winter. In case that extreme gear oil is in short supply, engine oil 50# in summer and engine oil 40# in winter may be used instead.
* For reducers newly put into use, tighten the fastening parts after 24h’ operation; tighten them again after 7-day’ operation, and one more time after 30-day’ operation.
* In normal operation, check whether oil leakage happens at the bearing cap of the reducer, shaft end seal, the contacting surface of the casing of the reducer, plug for oil drain hole, also check if the fastening pieces become loosen.
* Clean the inside of the reducer that has newly operated for 6 months, replace the lubrication oil.
* Maintain the reducer in normal operation. The user should carry out an overall maintenance after 6-12 months of operation according to the practical working conditions, including the following: Open the check hole cover, check the worn condition of each gear pair, observe and analyze the lubrication oil. If the lubrication is found to have gone bad, it should be drained and cleaned completely with thin oil and refill new lubrication oil. In case the reducer is not to work at once, the pumping unit should run at least 10 minutes to ensure that the oil film forms on the surface of the gear tooth and the bearing of the reducer.
* Strictly carry out the above Item 1, 2 and 3 for mandatory maintenance of the reducer according to SY/T5044-2003 “Walking Beam Pumping Units”
Model and size
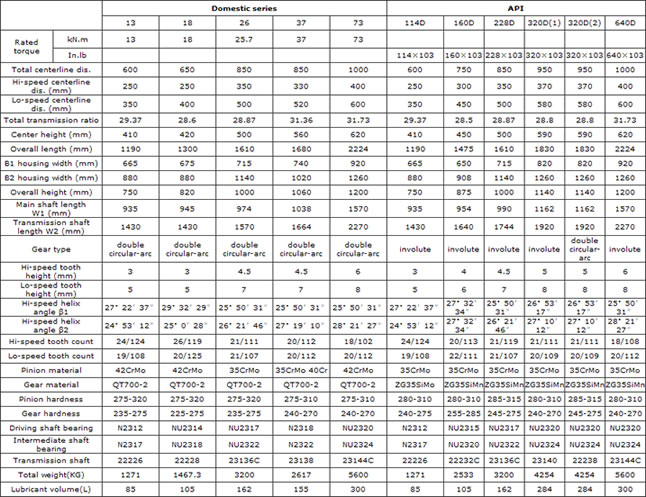
General fault, cause and measure to take
No. |
Fault |
Appearance |
Causes |
Prevent and measure to take |
1 |
The gear and bearing rust seriously |
|
1. In the moist environment, discontinuity on and off, water in housing, unsuitable lubrication or gone bad. 2. inadequate vent. |
1. Drain the used oil, clean and replace suitable lubrication. 2. Check out the breath hole, make it through. |
2 |
Gear is pitting bruised continuously and seriously (if pitting appearance shortly over, it is normal.) |
|
1. Reducer runs overload. 2. Lubrication unconformity the technical specification requirements. 3. Lubrication lose lubricate ability, lube is emulsified by the water or polluted by impurity. |
1. Decrease load, adjust balance weight. 2. According to the technical specification, to select suitable lubrication. 3. Replace new lubrication. |
3 |
Bearing and the parts run abnormal and galling |
Check if bearing heated and noise on the bearing socket |
1. Lubricate inadequate or the oil polluted by the metal impurity. 2. Bearing unmatched. 3. Reducer overloaded, bearing and gear wore. 4. Bearing and sealing piece loosen and cause damage. |
1. Add lubrication, adjust the gap between oil scraper and gear or replace new oil. 2. Adjust bearing moving gap within 0.25-0.5 mm. 3. Decrease the load, adjust balance weight. 4. Tightening the bolt on the cover and the connection parts. |
4 |
Transmission gear axial drifting |
Hammering in reducer |
1. Loosen between the gear and shaft. 2. Bearing is damaged. |
1. Replace the gear and transmission gear. 2. Replace bearing. |
5 |
Lube oil to gear and flow into the bearing groove too little |
|
1.the oil is too thin on the high temperature, too thick on the low temperature. 2.oil level too low. |
1. Replace suitable viscosity oil. 2. Add the oil up to suitable level. |
6 |
The reducer is over-heated |
The temperature of lube exceeds 70°C |
Too much lubrication, viscosity is not suitable. |
Decrease the lubrication to make the oil surface down to suitable level, change the lubrication oil brand. |
7 |
Reducer oil leakage |
Each sealing area |
1. Bolt loosen, large particles solid impurity in the sealant between contacting surfaces. 2. Shaft end sealing damaged. 3. Blocking in oil return hole and air vent. |
1. Screw down the bolt, replace sealant. 2. Replace the sealing piece. 3. Dredge the oil return hole and the air vent. | |